Plastic & Extrusion Line Cooling Rollers
Siva Engineering Works, is a trusted name in the manufacturing of Plastic & Extrusion Line Cooling Rollers based in Ahmedabad, Gujarat, India. Our cooling rollers are designed to optimize the cooling process in various plastic extrusion applications, ensuring consistent quality and efficiency in production. With a commitment to excellence, we cater to a wide range of industries, providing innovative solutions that enhance operational performance.
Plastic and extrusion line cooling rollers are critical components used in the extrusion process of plastic materials. During extrusion, plastic is heated and forced through a die to create a specific shape. As the extruded plastic exits the die, it needs to be cooled rapidly to maintain its shape and quality. Cooling rollers facilitate this process by providing a controlled cooling environment, allowing the extruded material to solidify properly while maintaining its dimensional integrity.
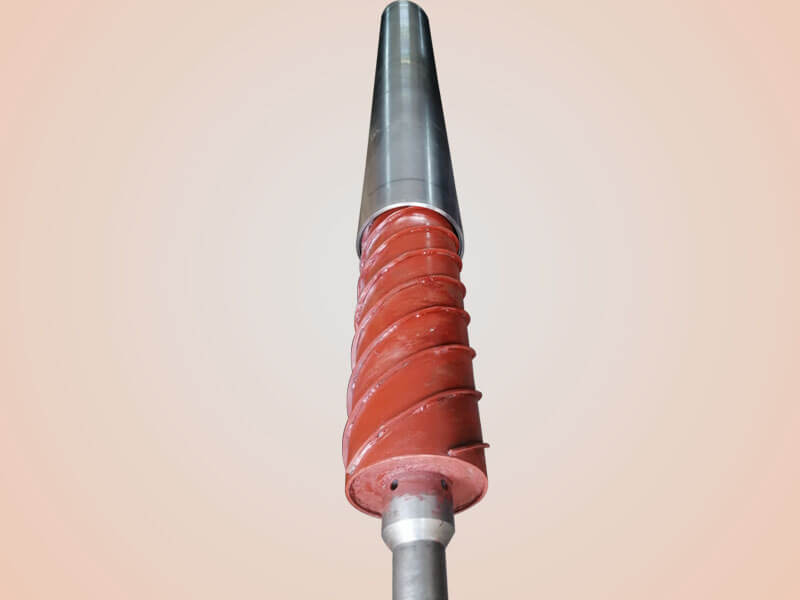
Key Features of Our Plastic & Extrusion Line Cooling Rollers
Efficient Cooling
Our cooling rollers are engineered to provide effective heat dissipation, ensuring that extruded materials cool uniformly and quickly.
Durability
Made from high-quality materials, our cooling rollers are designed to withstand the rigors of the extrusion process, ensuring long-lasting performance.
Customizable Design
We offer customizable cooling roller designs tailored to meet specific production needs, including various sizes, materials, and cooling configurations.
High Precision
Our rollers are manufactured with precision to ensure uniform cooling across the entire surface, which is crucial for maintaining the quality of the extruded products.
Easy Maintenance
The design of our cooling rollers allows for easy maintenance, ensuring minimal downtime during production.